Options in FLAC3D are sold separately from the code license, allowing users to extend the program’s capabilities as meets their own analysis needs. Modules available as options for FLAC3D include: Cluster Computing, IMASS, Dynamic, Creep, and Thermal.
Cluster Computing
The Cluster Option (FLAC3D only) allows users to speed up the solving process by launching multiple connected FLAC3D instances in cluster computing environments.
Cluster computing is a type of computing where multiple computers are connected as a cluster and execute operations together as a single entity. Software on each node (computer acting as a server in a cluster) does the same task simultaneously and coordinates the use of many processors using parallel computing techniques, which provides enhanced computational power and resolves the demand for content criticality and process services in a faster way.
The Cluster option in FLAC3D utilizes its cluster computing mode under a leader-follower architecture. Each node in the cluster network runs a FLAC3D instance, and all the FLAC3D instances are connected through Message Passing Interface (MPI) for data communication and management.
A significant speedup can be achieved for the solving process. For example, a model with 8 million zones on multiple nodes using the cluster option performs about 20 times faster on 32 nodes. The Cluster option has three plan levels depending on the number of nodes to be utilized: 8 nodes (Basic plan), 16 nodes (advanced plan), and 32 nodes (professional plan).
The cluster option in FLAC3D does not affect the results. FLAC3D generates results identical to normal runs with the same level of accuracy and determinism. The save files are also cross-compatible between normal FLAC3D and the cluster option.
Currently supported FLAC3D features:
- Continuous mechanical analysis with both small and large strain configurations
- Discontinuous mechanical analysis with zone joints (small strain)
- Excavations with apply relax conditions and backfill
- Dynamic analysis
- Fluid undrained pore pressure response
- General FISH callback functionalities
- All ITASCA constitutive models
- Factor-of-safety analysis
- General FLAC3D model and post-processing workflows
- Local model partial visualization via FLAC3D GUI version
- Result determinism
LEARN MORE about Cluster Computing for FLAC3D.
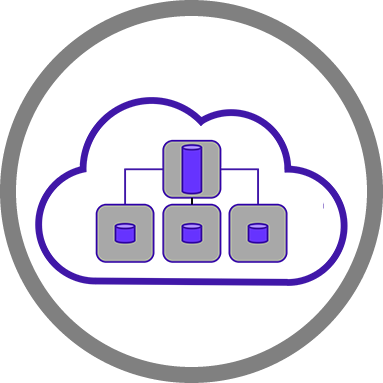
IMASS
The Itasca Constitutive Model for Advanced Strain Softening (IMASS) has been developed to represent the rock mass response to excavation induced stress changes. IMASS represents the damage around an excavation, slope, or caving process by accounting for the progressive failure and disintegration of the rock mass from intact, jointed, and/or veined rock to a disaggregated, bulked material. IMASS is based on empirical relationships and uses strain and zone-size dependent properties that reflect the impacts of dilation and bulking as a rock mass undergoes plastic deformation.
IMASS uniquely contains two softening (or residual) yield envelopes to represent the two-stage softening behavior for a rock mass that distinguishes between damage (caused by fracturing and the associated loss of cohesion and tensile strength) and the subsequent disturbance (due to bulking) in rock mass behavior. This two-stage softening/weakening behavior in IMASS is critical to accurately represent the rock mass post-peak behavior for underground and surface mining applications.
IMASS is available as a built-in, optional constitutive model for FLAC3D (version 7.0 or later) and is sold as a separate, monthly or annual lease, license.
LEARN MORE about IMASS for FLAC3D.
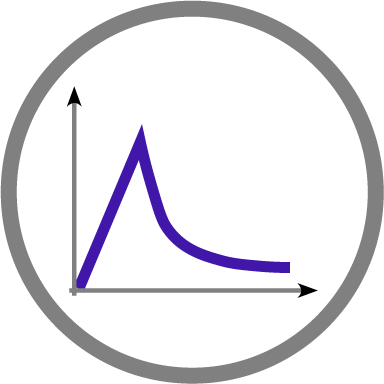
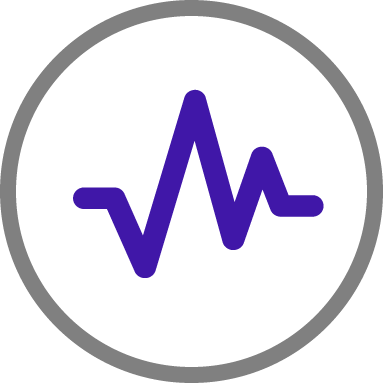
DYNAMIC OPTION
The dynamic analysis option permits three-dimensional, fully dynamic analysis with FLAC3D. User-specified acceleration, velocity, or stress waves can be input directly to the model either as an exterior boundary condition or an interior excitation to the model. FLAC3D contains absorbing and free-field boundary conditions to simulate the effect of an infinite elastic medium surrounding the model.
This option can be coupled to the structural element model, thus permitting analysis of soil-structure interaction brought about by ground shaking. The dynamic feature can also be coupled to the groundwater flow model. This allows, for example, analyses involving time-dependent pore pressure change associated with liquefaction. The dynamic model can likewise be coupled to the optional thermal model in order to calculate the combined effect of thermal and dynamic loading. The dynamic option extends FLAC3D's analysis capability to a wide range of dynamic problems in disciplines such as earthquake engineering, seismology, and mine rockbursts.
LEARN MORE about FLAC3D's dynamic modeling capabilities.
CREEP OPTION
This option can be used to simulate the behavior of materials that exhibit creep (i.e., time-dependent material behavior).
There are eleven available material models in FLAC3D that simulate viscoelastic and viscoplastic (creep) behavior:
- Maxwell model — A classical viscoelastic model known as the Maxwell substance.
- Burgers model — A classical viscoelastic model known as the Burgers substance, composed of a Kelvin model and a Maxwell model.
- Power model — A two-component power law model used for mining applications (e.g., salt or potash mining).
- WIPP model — A reference creep model commonly used in thermomechanical analyses associated with studies for the underground isolation of nuclear waste in salt.
- Burgers-Mohr model — A viscoplastic model combining the Burgers model and the Mohr-Coulomb model.
- Power-Mohr model — A viscoplastic model combining the two-component power model and the Mohr-Coulomb model.
- Power-Ubiquitous model — A viscoplastic model combining the two-component power model and the ubiquitous-joint model.
- WIPP-Drucker model — A viscoplastic model combining the WIPP model and the Drucker-Prager model.
- Soft-Soil-Creep model — A soft soil model considering the time-dependent secondary compression.
- WIPP-Salt model — A viscoplastic model modified from the WIPP model; includes volumetric and deviatoric compaction behavior for salt-like materials.
- Columnar-Basalt (COMBA) Model — The Columnar-Basalt (COMBA) model accounts for the presence of up to four arbitrary orientations of weakness (ubiquitous joint) in a non-isotropic elastic matrix. NEW
All eleven models are available with the creep option. A FLAC3D grid can be configured for both a creep calculation and a dynamic calculation. However, both models are generally not used simultaneously because of the widely different timesteps.
In addition, it is also possible for users to write their own creep constitutive models using the C++ UDM option.
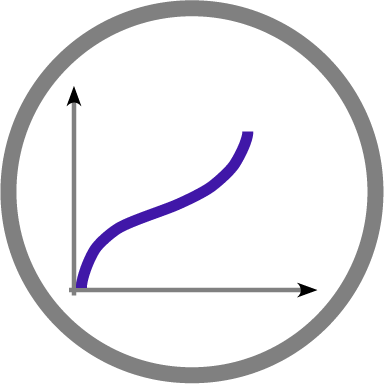
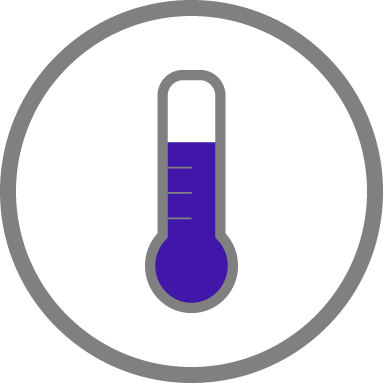
THERMAL OPTION
The thermal option of FLAC3D incorporates both conduction and advection models. The conduction models allow simulation of transient heat conduction in materials, and the development of thermally induced displacements and stresses. The advection model takes the transport of heat by convection into account; it can simulate temperature-dependent fluid density and thermal advection in the fluid. This thermal option has several specific features:
- Four thermal material models are available: isotropic conduction, anisotropic conduction, isotropic conduction/advection, and the null thermal model.
- As in the standard version of FLAC3D, different zones may have different models and properties.
- Any of the mechanical models may be used with the thermal model.
- Temperature, flux, convective and adiabatic boundary conditions may be prescribed.
- Heat sources may be inserted into the material as either point sources or volume sources. These sources may decay exponentially with time.
- Both explicit- and implicit-solution algorithms are available.
- The thermal option provides for one-way coupling to the mechanical stress and pore-pressure calculations through the thermal expansion coefficients.
- Temperatures can be accessed via FISH for users to define temperature-dependent properties.
HYDRATION
Hydration is defined as the chemical absorption of water into a substance, a process by which heat is generated (hydration heat). The setting of concrete (which can be considered as a transition from liquid to solid phase) is the most relevant example for the hydration process in the engineering world.
The effects of the hydration process can be separated into different physical parts, where the thermal and mechanical parts are the most relevant. The implementation of hydration models in FLAC3D follows this separation, as the hydration heat generation and heat transfer are dealt with in thermal models, material hardening and strength development are implemented as constitutive models of mechanical behavior. The hydration model is based on a procedure that considers empirical rules, theoretical considerations, and practical experiences (Onken and Rostásy 1995).
A thermal hydration constitutive model is implemented in FLAC3D. For simulating a hydration process, a mechanical constitutive model that can adjust the mechanical properties corresponding to the hydration grade (or equivalent concrete age) is also required. The Hydration-Drucker-Prager model is provided to handle those mechanical aspects.
Onken, P., and F. Rostásy. Wirksame Betonzugfestigkeit im Bauwerk bei früh einsetzendem Temperaturzwang, DAfStb Heft 449. Berlin: Beuth-Verlag (1995).